私たちの製品が一体どんな風に作られているのか、ECスタッフが実際に生産現場を訪問した「ものづくり工場見学inフィリピン」。後編では、バッグのものづくりの原点でもある、野球グローブの生産現場を訪ねました。
>前編はこちら
野球グローブのものづくり
バッグのものづくりを見学した次の日は、野球グローブの生産現場へ。
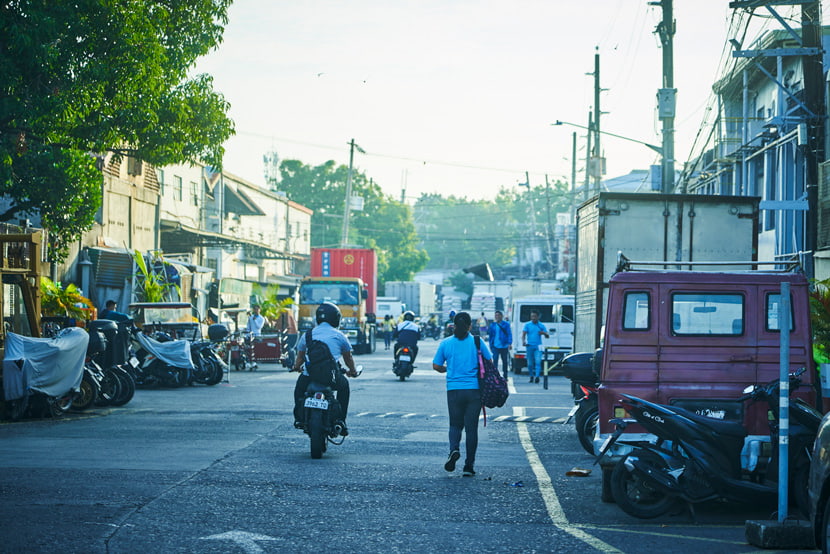
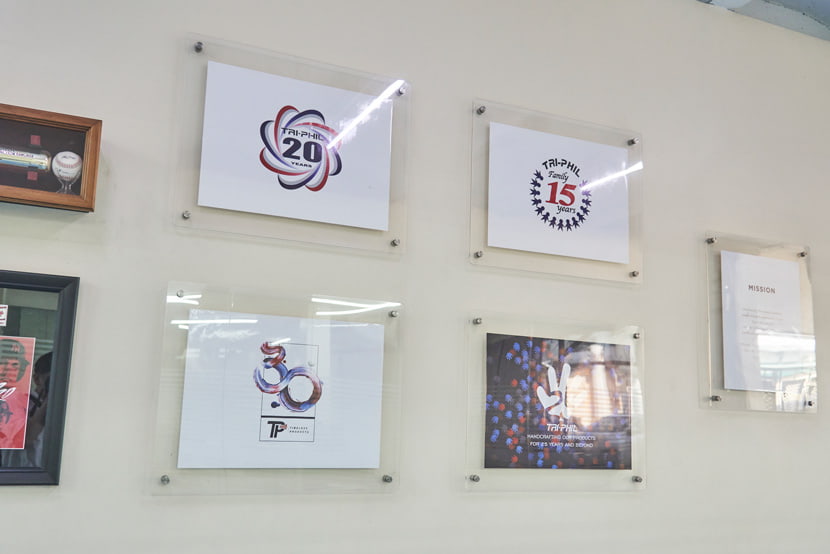
世界的なメーカーのOEM製品を生産している野球グローブ。その作りはとても複雑かつ緻密で、約30以上ものパーツを組み合わせていくことで完成します。
工程のほとんどが人の手作業という技術と経験が不可欠な中、トライフィルでは手工芸である製品を、手工業として均一に作り上げるシステムを構築してきました。
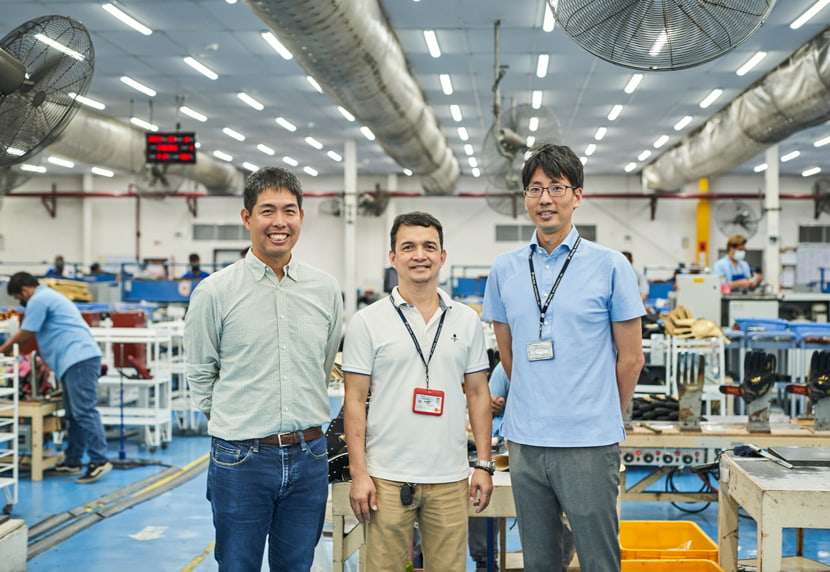
圧巻の保存倉庫
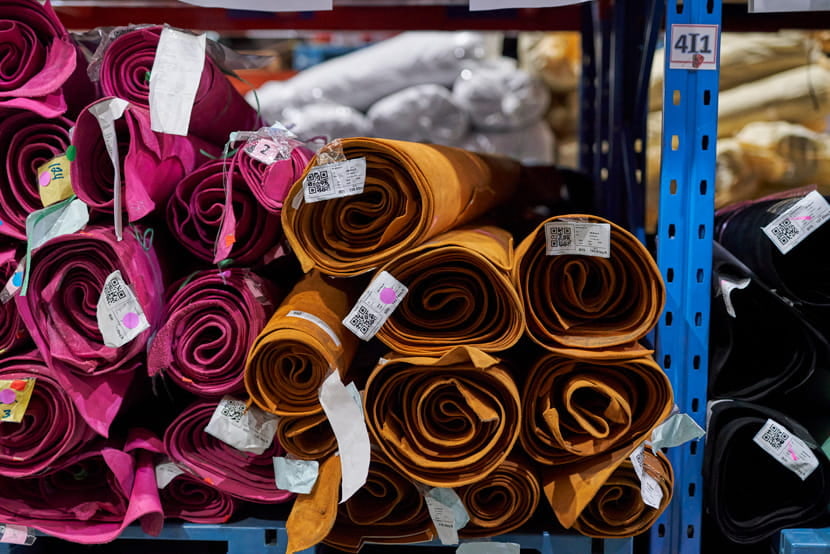
まず最初に案内してもらったのが、私たちの核となるグラブレザーの保管倉庫。気温と湿度を一定に保った空間に、整然と並べられていました。
野球グローブの工程
バッグ以上の緻密な工程によって作られる野球グローブ。その工程をほんの一部ですがお見せします。
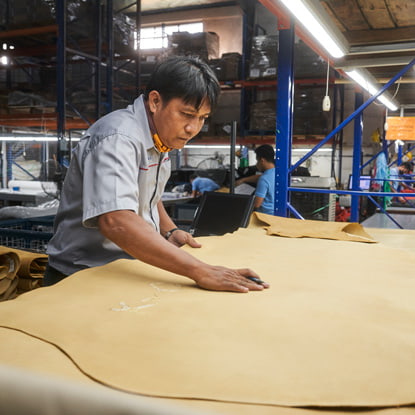
1.革の検品
まず要になる、グラブレザーの検品。タンナーから送られてきた高グレードの革を、さらに私たち独自の基準で厳しく選別していきます。

2.裁断
金型を使って裁断していきます。この工程で余った革が、残革としてPANELシリーズの素材となっていきます。
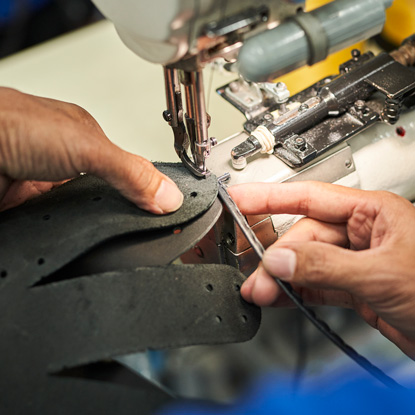
3.指のまとめ
裁断した革を「漉き」で一定の厚みにしたあと、刻印や刺繍などを得て、いよいよ組み立て(縫製)がはじまります。
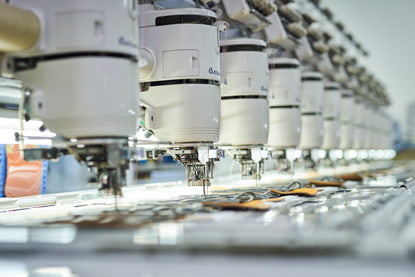
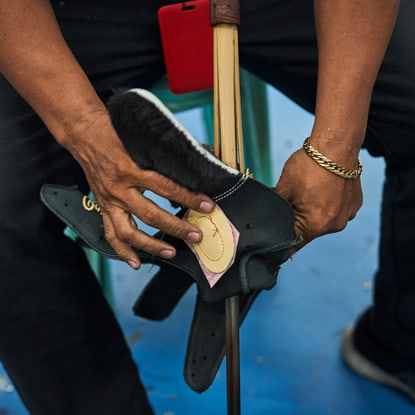
4.ひっくり返し
強度を保つため縫い目が表に出ないよう、裏面から縫い合わせ、最後にひっくり返す工程です。この工程もバッグ作りに受け継がれています。昔ながらの竹を使った工具が一番使いやすいそう。
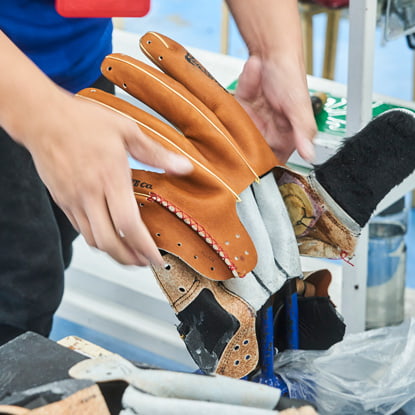
5.裏入れ
手を入れる内手袋と球を補給する外手袋の二重構造を合わせていき、その後バインディングと呼ばれる縫製を行います。
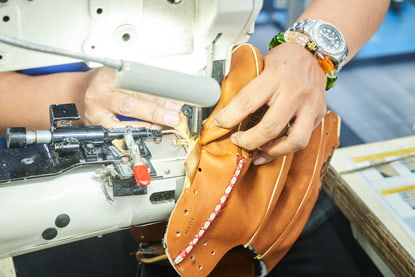
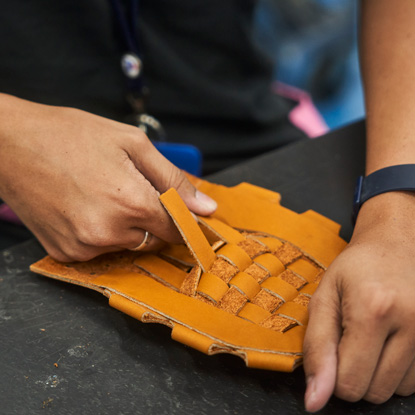
6.ウェブ製作
親指と人差し指の間にあたるウェブ部分の組み立て。ちょうどバスケット編みを行なっていました。この他にもグローブに合わせた様々な形のウェブを組み立てます。
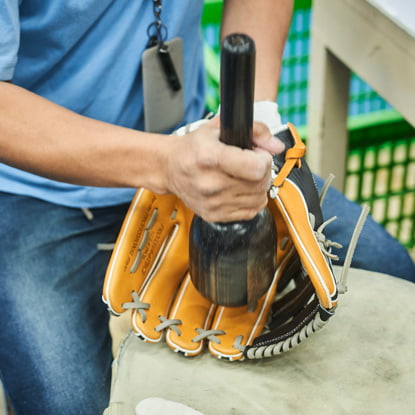
7.仕上げ工程
組み立て後、手に馴染むようマシンで叩いて革を馴染ませ柔らかくします。最後は人の手で叩いて微調整。
その後、検品や品質テストなど最終工程を経て完成します。
独自のトライオン品質
職人の腕による手工芸品の品質を維持したまま大量生産へと導くため、トライオンでは独自の生産テクノロジーを構築。すべての工程を一つずつに分解してマニュアル化し、技術者育成と徹底した品質管理を実施。細部まで手作業で正確に、かつ均一な品質で作る「トライオン品質」を維持しています。
【番外編】トライフィルの勤続年数表彰式へ
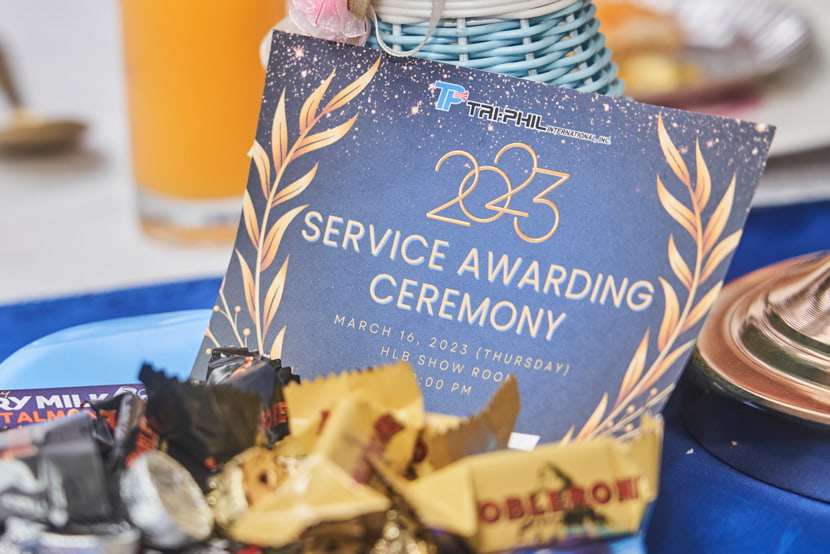
私たちが訪問していた時にちょうど、勤続年数表彰式が開催されていました。長く勤めてくれるスタッフに対して、これまでの労いを込めた催しです。今回その催しに、飛び入り参加させて頂きました!
和気あいあいとした雰囲気の中、勤続年数ごとに受賞者のスピーチと記念品授与が行われていきます。
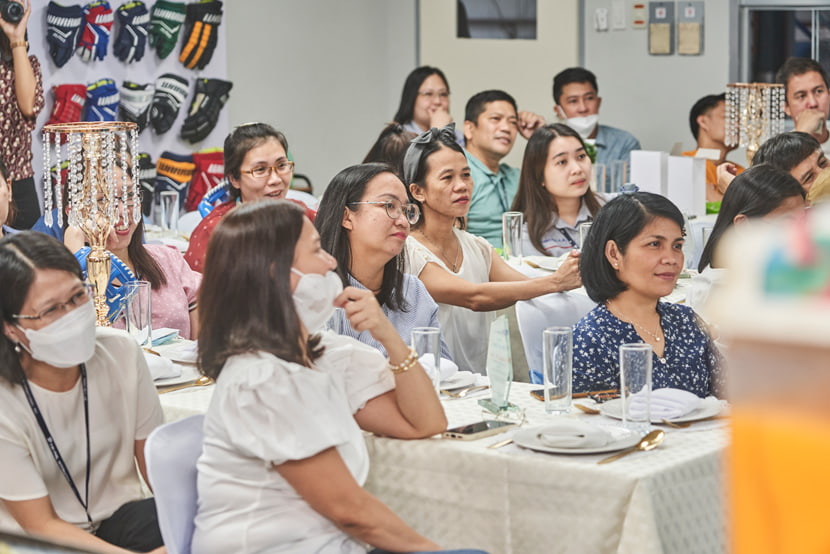
受賞者の最後に呼ばれたのが、トライフィル社長、ジョシーさん(Ms.Josie)。トライフィル創設と共に入社し、2005年からトライフィルの社長に就任。名前が呼ばれた瞬間、今日一番の拍手喝采が。スタッフたちから愛されている方なのを感じます。
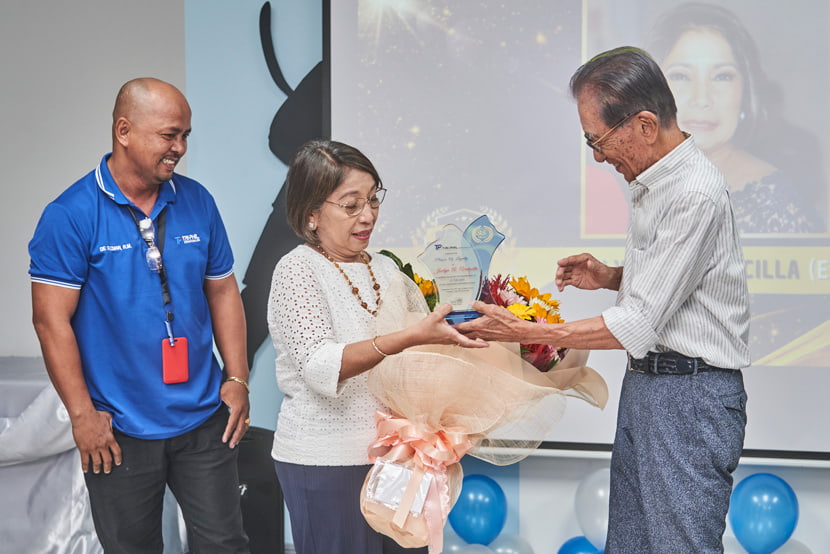
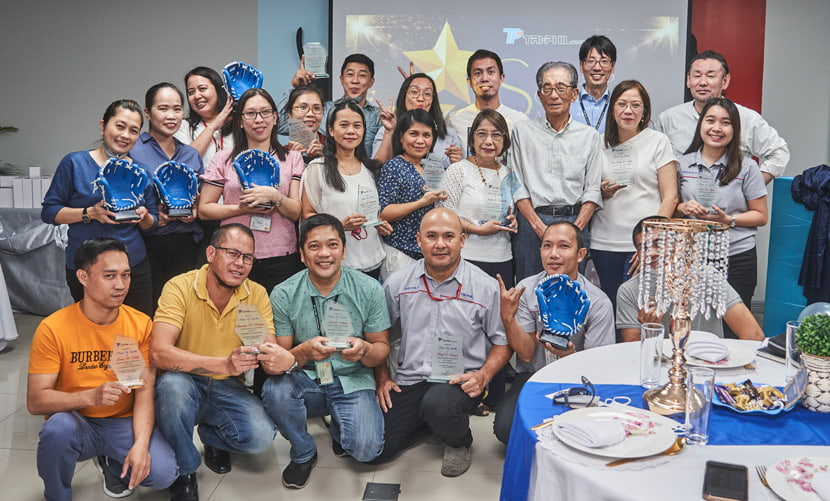
このような催しなど福利厚生の充実や、働きやすい環境作りを積極的に行っているトライフィル。従業員を大切にし、固い信頼関係を築き上げています。
見学を終えて
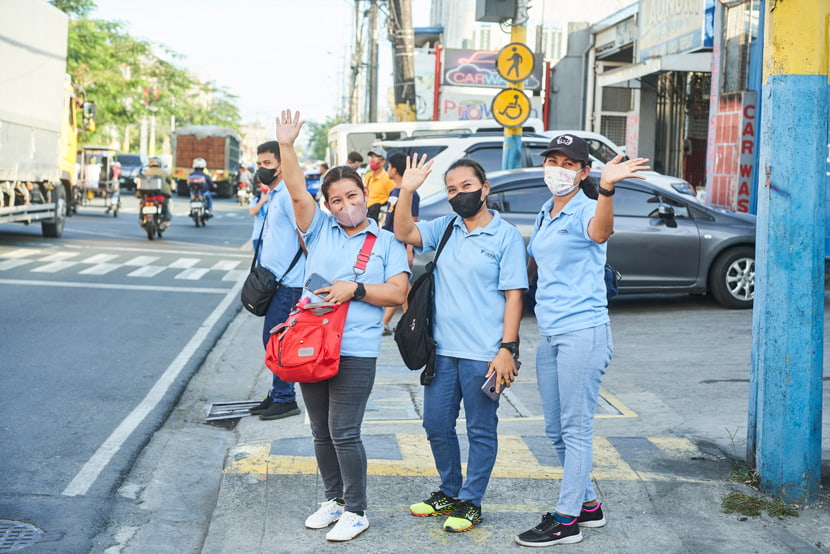
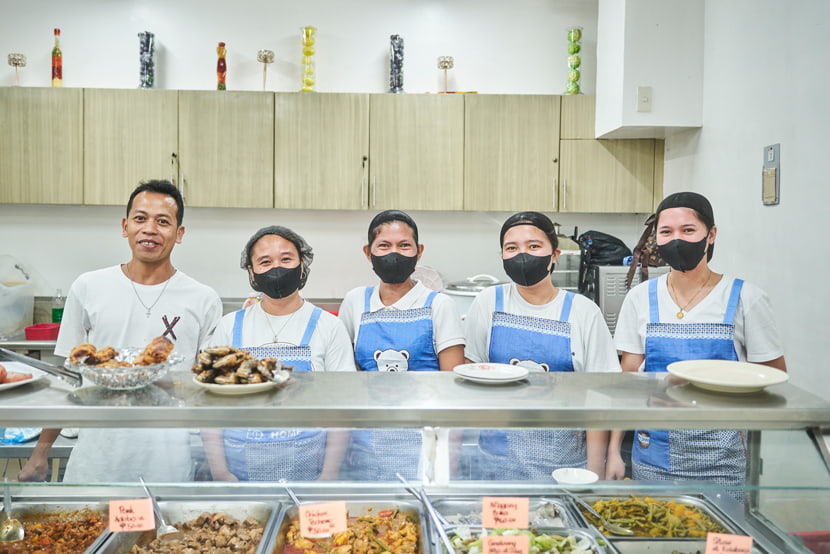
初めて訪れたフィリピンは、南国らしい陽気な空気感と、屈託のない笑顔が素敵なフレンドリーな人々が印象的で、そんなHAPPYな人たちの手によってものづくりが行われていました。
私たちの製品は、機械ではなく人の手でしか作れないものであり、クラフトマンシップによって成り立つものづくりです。そのことを私たちは「People's Business」と呼んでいます。その言葉を、実際に現場に立つことで肌で実感することができました。
トライオンとトライフィル、そしてベトナムのトライベト。多くの人の手による「People's Business」から生まれた私たちの製品を、これからも皆さまの手元で、愛着を持って使い続けていただけることを願っています。